About Me
Places I have worked
Research Assistant at Center for Energy Efficiency and Renewable Energy from Sep 2019 to Jan 2023
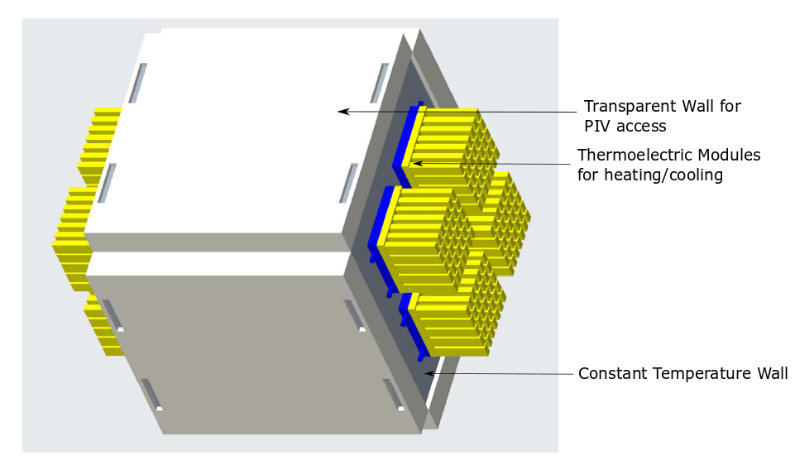
I study Latent Heat Thermal Energy Storage Systems(LHTES), with a focus on creating physics infused performance
correlations (inspired by flow physics rather than curve fit) for LHTES devices. I conduct combined numerical and experimental studies to support my
hypotheses. Our research will help reduce electric demand when used in conjunction with combined heat and power plants. It shall also be used to
integrate renewable energy sources like solar thermal with the grid. Our basic fluids research(conducted as part of this project) will improve our
understanding of turbulent natural convection. For our project proposal entitled “Design of Latent Thermal Energy Storage Heat Exchangers for
Combined Heat and Power Plants”, me and my collaborators Prof. Dragoljub (Beka) Kosanovic and Prof. Steve de Bruyn Kops were awarded the
Industrial Assessment Center (IAC) Award for Excellence in Applied Energy Engineering Research
2020 ! Thanks to Beka and Steve for guiding me in writing this proposal.
Graduate Intern at National Renewable Energy Laboratory from Feb 2021 to Aug 2021
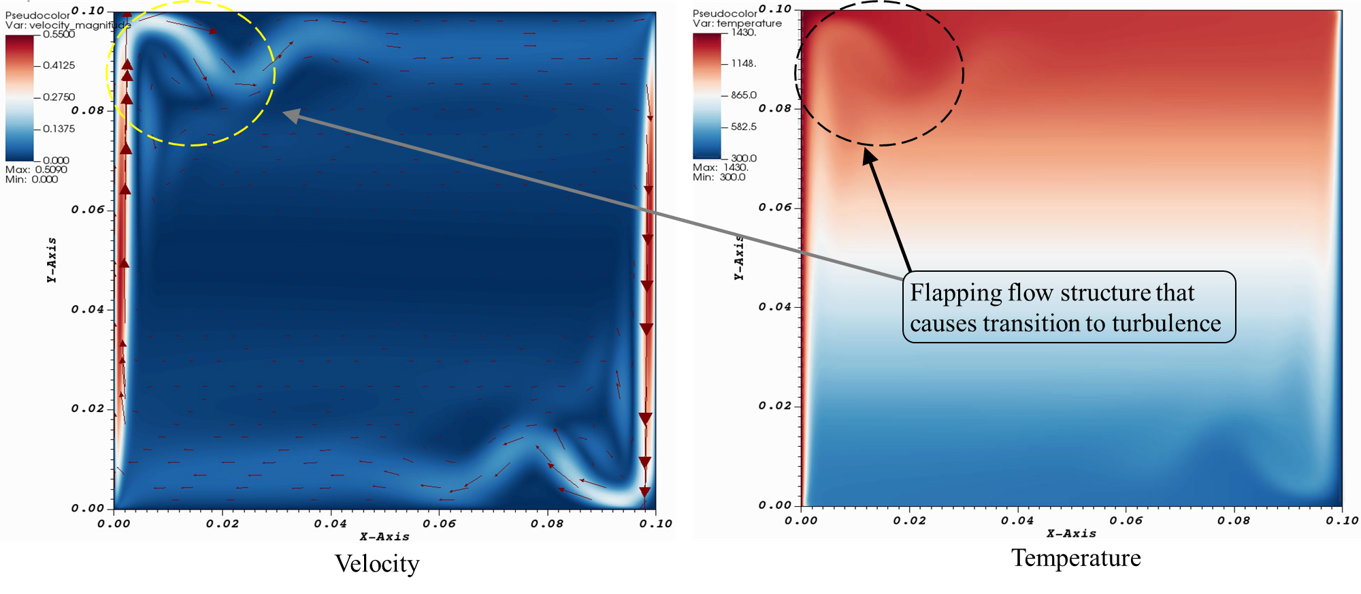
At NREL, I worked on the characterization of thermal resistances of PCM based thermal energy storage (TES) and the effect of convection on heat transfer rates in LHTES.
We published an article from my work there, Measuring the Maximum Capacity and Thermal Resistances in Phase-Change Thermal Storage Devices. I also verified experimentally that latent heat transfer rate is constant for a significant period, and melted fraction varies linearly with time, as predicted in earlier model.
Research Assistant at Turbulence Simulation Laboratory from Oct 2016 to Dec 2018
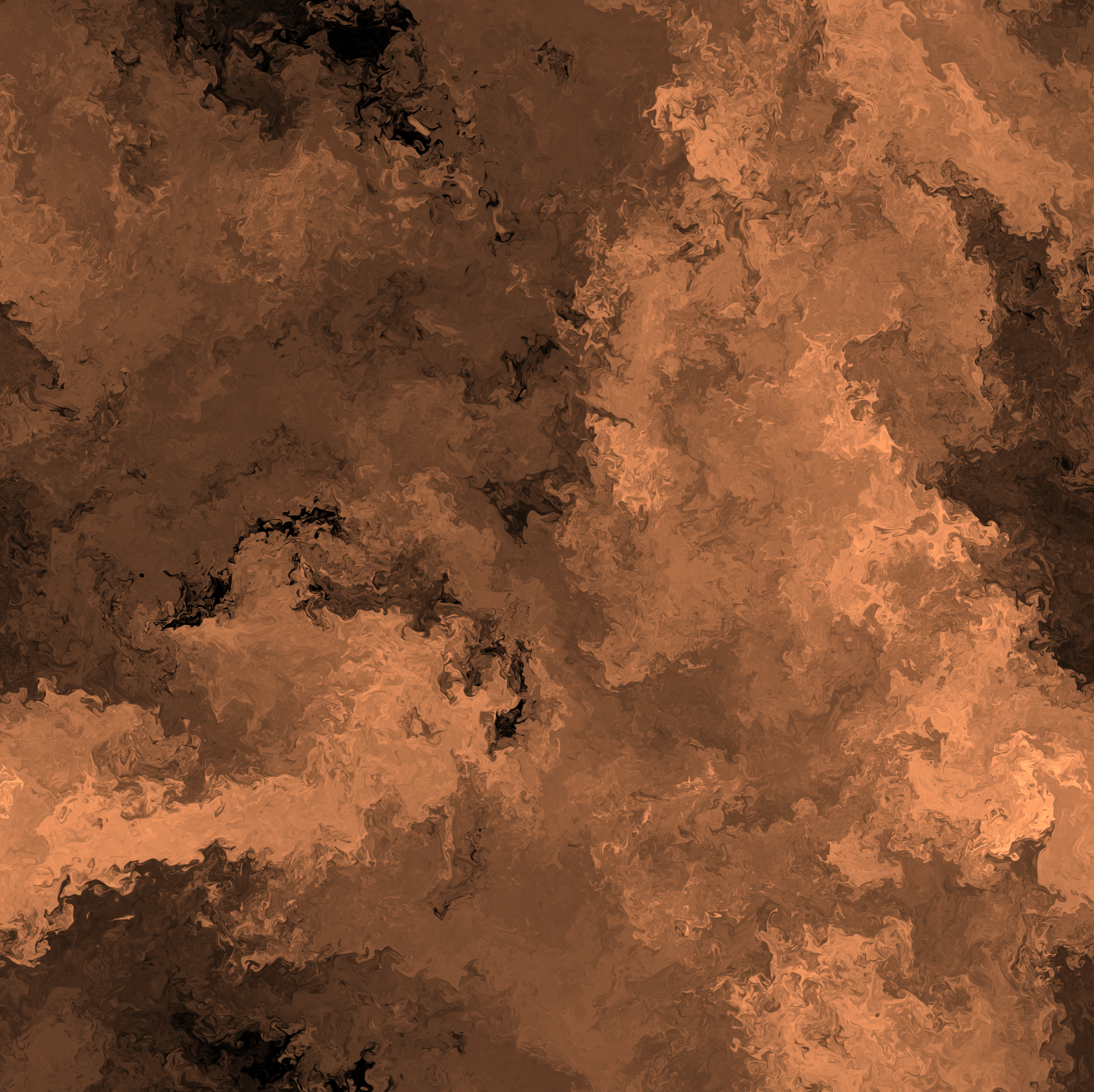
I studied turbulence and mixing using Direct Numerical Simulations (DNS). The mixing of scalars(such as temperature or chemicals) due to fluid turbulence is an important problem for modeling combustion, turbulent jets and geophysical flows. This fundamental research connects well to my LHTES research because heat transfer in LHTES devices is dominated by turbulent convection in the PCM.
Our results from this research are published in the Journal of Fluid Mechanics as Area of scalar isosurfaces in homogeneous isotropic turbulence as a function of Reynolds and Schmidt numbers and as my Master of Science thesis entitled Calculation of Scalar Isosurface Area and Applications. Thanks to Steve and Gavin for help and comments !
Energy Engineer at the Industrial Assessment Center (IAC) from Sep 2017 to Jan 2023
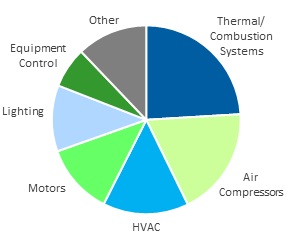
As the lead Energy Engineer at the Industrial Assessment Center, I have conducted over 30 energy assessments and saved customers over 8.9 million MMBTU’s equivalent of energy and $1,021,241 annually, metrics are available here, taken from the IAC portal. I have experience with conducting assessments independently, training new students and mentoring.
Senior Engineer at Thermax Ltd. from Mar 2016 to July 2016
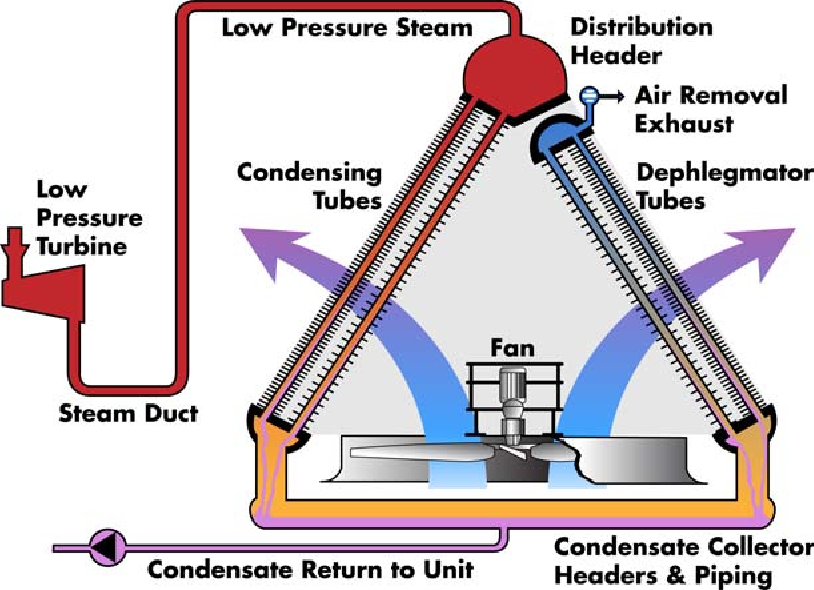
As senior engineer, I designed Air Cooled Condensers using the heat transfer software HTRI and validate by design procedure against experimental data for 50 existing Air Cooled Condensers across the world(provided by Thermax SPX). Our project was focused on predicting heat transfer rates for tubes at various inclinations, fin pitch and length, which is a two phase turbulent heat transfer problem, making it tough to study numerically. We thus approached it using standard correlations available in literature and HTRI, and tuned our formulation to match experimental results provided by Thermax SPX.
Application Engineer at SKF Ltd. from Jun 2014 to Sep 2015
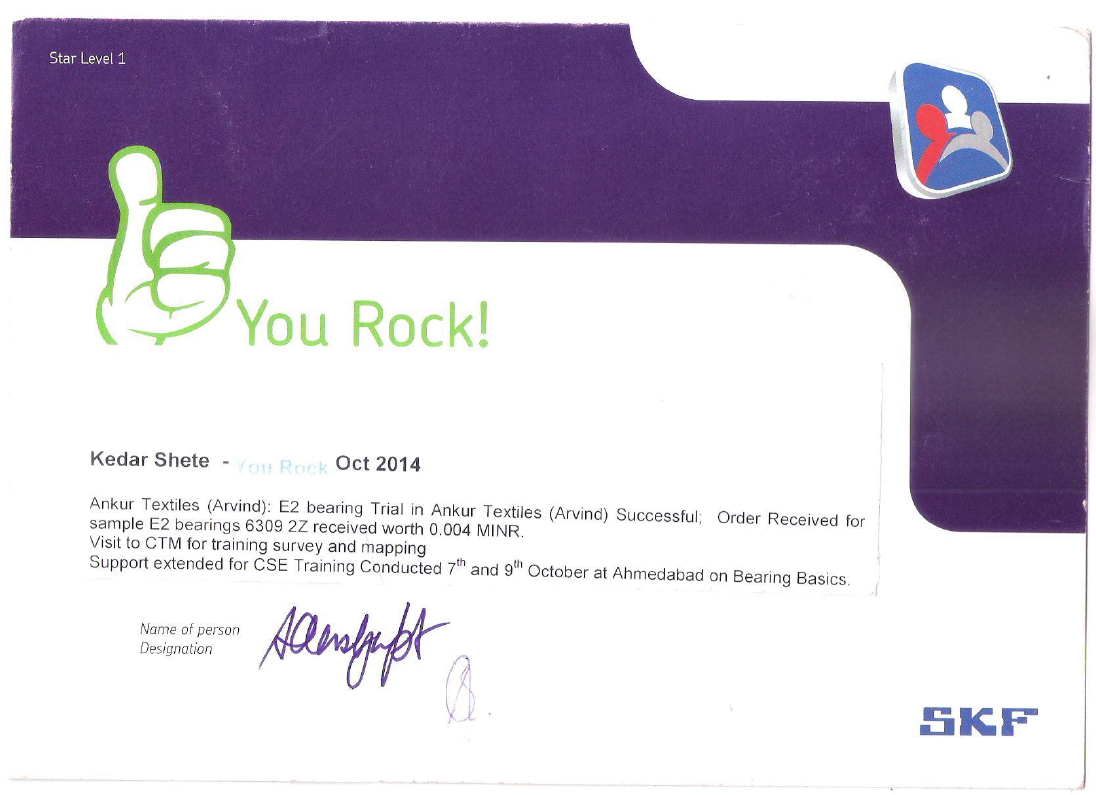
As Application Engineer at SKF India Ltd, I worked for 6 months in the after market business, where I designed bearing systems for the after market customers. After a period of 6 months, I was promoted to the OEM division, where I designed bearing and lubrication systems for manufacturers of crushers, vibrating screens, conveyors, motor and pump systems, transmission boxes, gearboxes, etc. The certificate shows an achievement award for a project I lead, entitled “Improvement in energy efficiency of Ring Frame Spinning Machines at Arvind Mills, 2014”.
Undergraduate Researcher at BITS Pilani KK Birla Goa Campus from Jan 2014 to Aug 2014
I increased the mixing and combustion efficiency in Circulating Fluidized Bed(CFB) risers using novel distributor plate designs. Circulating Fluidized Bed risers have applications in high efficiency boilers, gasifiers, combustors, dryers, power coating etc. When used as a boiler, they are accompanied by cyclone separators (to remove particulate matter prior to exhaust). Cyclone separators also have applications in the cement industry, waste water treatment, boilers technology and even vacuum cleaners. I also proposed alternative cyclone separator designs to enable heat extraction from cyclone separators, using internal fins. Our results were published as Effect of Novel Swirling Perforated Distributor on Fluid Dynamic Characteristics of Circulating Fluidized Bed Riser and two conference papers at 5th International Conference on Fluid Mechanics and Fluid Power (FMFP 2014)
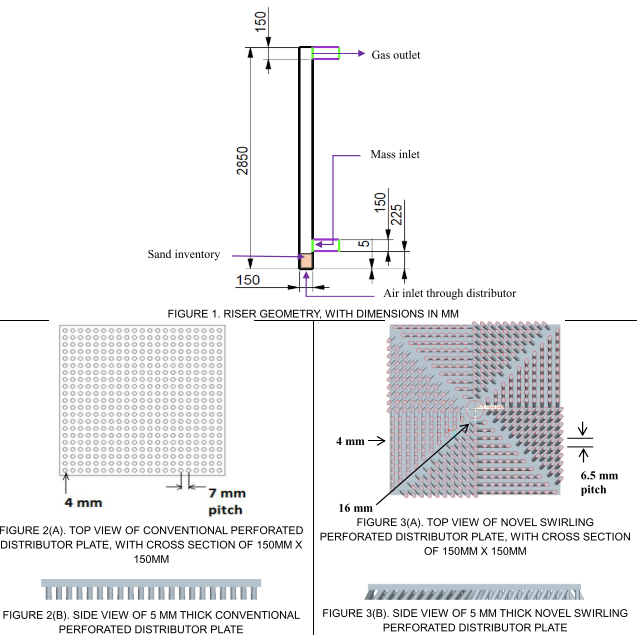
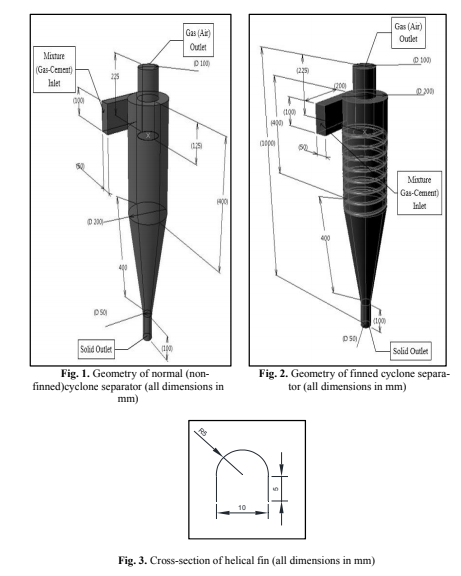